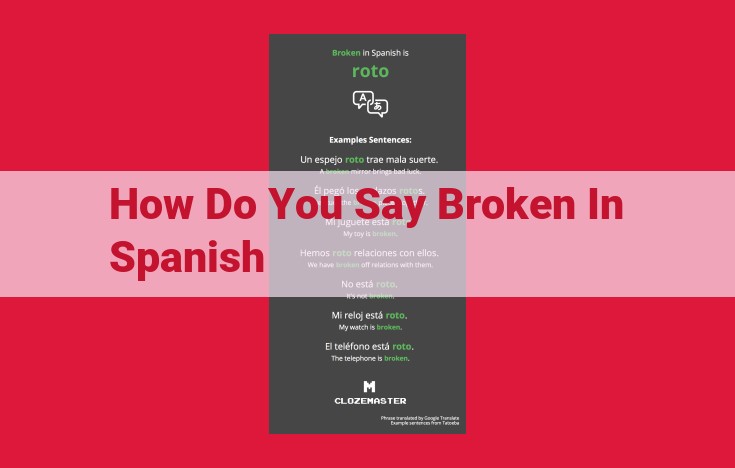
Understanding Breakage: Spanish Terminology And Usage
En español, "roto" es el término más común para expresar el concepto de algo quebrado. También se pueden utilizar palabras como "fracturado", "dañado" o "averiado" para describir diferentes tipos de roturas. Para indicar que algo está roto, puedes utilizar frases como "está roto" o "se rompió".
- Define breakage and its importance in various industries.
- Overview of the outline and its purpose.
Breakage: A Bane in Every Industry
Breakage, or the unwanted and often sudden rupture of an object, can be a costly and frustrating occurrence in countless industries. Whether it's a broken machine in a factory, a shattered window in a building, or a damaged product during shipping, breakage can have significant consequences.
Recognizing the Importance of Breakage Management
Understanding the concept of breakage is crucial for businesses and individuals alike. Its importance stems from the potential risks and costs associated with it. Broken equipment can lead to safety hazards, prolonged downtime, and repair expenses. Damaged products can result in dissatisfied customers, lost revenue, and reputational damage. Therefore, it's imperative to recognize the significance of breakage management for both safety and economic reasons.
Delving into the Outline: A Comprehensive Guide to Breakage
This blog post will provide an in-depth analysis of breakage, guiding you through its various types, causes, consequences, and management strategies. We'll explore real-world examples through case studies, highlighting best practices and lessons learned. By the end, you'll be equipped with the knowledge to mitigate breakage risks and minimize its detrimental impact on your business operations or daily life.
Types of Breakage
- Nouns: Ruptura, fractura, daño, avería, rotura, falla, quebrantamiento
- Verbs: Romper, fracturar, dañar, averiar, quebrar, fallar
- Phrases: Estar roto, romperse, romper algo, arreglar algo roto, pieza rota
- Adjectives: Roto, fracturado, dañado, averiado, quebrado, fallo
Types of Breakage
Breakage, a term often used to describe something broken, shattered, or malfunctioning, can manifest in a myriad of ways. Understanding these different types can help us identify, prevent, and manage breakage more effectively.
Nouns of Breakage
Words like rupture, fracture, damage, failure, and quebrantamiento capture the essence of breakage as a state of being. They describe a loss of integrity, a separation, or a disruption in structure or function.
Verbs of Breakage
Verbs like romper, fracturar, and quebrar actively depict the process of breakage. They convey the act of causing something to break or stop working, whether through physical force, wear and tear, or internal defects.
Phrases of Breakage
Phrases such as estar roto (to be broken), romperse (to break), and arreglar algo roto (to fix something broken) provide context and detail to breakage. They describe the condition of an object or system that has experienced breakage, as well as the actions taken to address it.
Adjectives of Breakage
Adjectives like roto (broken), dañado (damaged), and fallado (failed) modify nouns to indicate the state of breakage. They help us visualize and understand the extent and nature of the damage, whether it's a small crack, a complete fracture, or a total malfunction.
Causes of Breakage: Understanding the Root of the Problem
When it comes to maintaining the integrity of equipment, machinery, and infrastructure, breakage poses a significant challenge. Understanding the underlying causes of breakage is crucial for implementing effective prevention and management strategies.
Mechanical Stress:
This refers to the physical forces exerted on a material or object, causing it to distort, deform, or fracture. Examples include excessive loading, bending, vibration, and impact. These forces can arise from normal operating conditions or external factors such as accidents or natural disasters.
Material Defects:
Imperfections within a material can significantly weaken it, making it more susceptible to breakage. These defects may be inherent to the material's composition or introduced during the manufacturing process. They can include cracks, inclusions, voids, and variations in grain structure.
Environmental Factors:
Exposure to harsh environmental conditions can degrade materials over time, contributing to breakage. Factors such as extreme temperatures, humidity, corrosion, and radiation can accelerate the deterioration of materials. These conditions are particularly relevant for equipment and structures exposed to outdoor elements or harsh industrial environments.
Human Error:
Mistakes and oversights can lead to improper handling, maintenance, or operation of equipment and materials, increasing the risk of breakage. This can include improper installation, lack of proper maintenance, and failure to follow safety protocols. Human error is a common contributor to breakage, highlighting the importance of training and adherence to established procedures.
Consequences of Breakage
In the relentless pursuit of efficiency, reliability, and safety in various industries, breakage stands as a formidable adversary. Its consequences extend far beyond the mere repair or replacement of damaged components. Let's delve into the detrimental effects of breakage, unveiling its menacing grip on safety, finances, and efficiency.
Safety Risks
Breakage poses grave risks to human safety. In high-risk industries, such as manufacturing and construction, broken equipment can lead to catastrophic events. A malfunctioning part in a crane can cause it to collapse, endangering the lives of workers below. Similarly, broken electrical components can trigger fires or electric shocks, jeopardizing personnel safety.
Financial Losses
Breakage wreaks havoc on corporate budgets. Replacing damaged parts is often costly and time-consuming. However, the financial losses extend beyond repair costs. Business downtime caused by breakdowns disrupts operations, resulting in lost productivity and revenue. In the healthcare industry, for instance, broken medical equipment can lead to delays in patient care, potentially costing hospitals millions in lost revenue.
Delays and Inefficiencies
Breakage also creates significant delays and inefficiencies. Broken machinery or components halt production lines, disrupting schedules and creating bottlenecks. In the transportation sector, a broken locomotive can cause train delays, affecting passenger travel and goods delivery. These delays ripple through supply chains, leading to disruptions and lost opportunities.
Recognizing these dire consequences, industries must prioritize comprehensive breakage management strategies to safeguard safety, protect finances, and ensure seamless operations.
Preventing Breakage: A Guide to Safe and Efficient Operations
Breakage can be a costly and dangerous issue in various industries, leading to safety risks, financial losses, and delays. Preventing breakage is essential to maintain optimal operations, ensuring employee safety, and maximizing profitability. This article will explore proven strategies for preventing breakage, focusing on proper design, quality materials, and regular maintenance.
Proper Design and Engineering:
The foundation of breakage prevention lies in sound design and engineering. When equipment and structures are designed with durability and functionality in mind, they are less prone to failure. This involves using appropriate materials, accounting for stress distribution, and incorporating safety features. By investing in well-engineered designs, you minimize the likelihood of breakage and enhance the overall performance of your systems.
Quality Materials and Manufacturing:
The choice of materials plays a critical role in preventing breakage. Opt for high-quality materials known for their strength, durability, and resistance to wear and tear. Employing advanced manufacturing techniques and quality control processes ensures that components meet specified standards, reducing the risk of defects and premature failure.
Regular Maintenance and Inspections:
Regular maintenance and inspections are vital to prevent breakage. Scheduled lubrication, adjustments, and cleaning extend equipment life by reducing wear and tear. Thorough inspections by qualified professionals identify potential issues early on, enabling timely repairs and preventing catastrophic failures. By adhering to a comprehensive maintenance program, you proactively address risks and keep your operations running smoothly.
Preventing breakage is an investment in the safety, efficiency, and profitability of your business. By implementing proper design and engineering, using quality materials and manufacturing, and conducting regular maintenance and inspections, you minimize the occurrence of breakage, protect your employees, reduce costs, and enhance the reliability of your operations. Remember, preventing breakage is not just a reactive measure but a proactive strategy that pays dividends in the long run.
Management of Breakage
Breakage, a common problem across industries, can lead to safety risks, financial losses, and operational inefficiencies. To effectively manage breakage, several strategies come into play:
Maintenance and Repair Strategies
Regular maintenance and inspections are crucial in preventing breakage. Inspecting equipment at scheduled intervals, identifying potential issues, and performing preventive maintenance can significantly reduce the risk of a breakdown. Establishing clear repair protocols and having a skilled maintenance team on standby ensures prompt and efficient repairs when breakage occurs, minimizing downtime.
Warranty and Insurance Coverage
Warranties provided by manufacturers offer protection against defects or malfunctions within a specified period. These warranties should be carefully reviewed and leveraged to cover potential repair costs. Additionally, insurance policies can provide financial protection against catastrophic breakage incidents, reducing the financial impact on businesses.
Service Contracts and Technical Support
Service contracts with equipment manufacturers or third-party service providers provide ongoing maintenance, repairs, and technical support. These contracts offer regular inspections and preventive measures to prevent breakdowns. Furthermore, they provide access to specialized technicians who can quickly resolve complex issues, reducing the need for costly repairs or replacements.
By implementing these management strategies, businesses can proactively address breakage, minimize its impact, and ensure the optimal performance of their assets. Early detection, prompt repairs, and effective management of breakage incidents contribute to safety, efficiency, and cost-effectiveness.
Case Studies: Breakage Management in Action
In the vast landscape of industries, breakage poses a significant challenge, leading to safety risks, financial losses, and operational setbacks. To illustrate the profound impact of breakage and showcase effective management strategies, we present real-world case studies that highlight the consequences and best practices associated with breakage control.
Case Study: Manufacturing Mishap
Incident: A manufacturing plant experienced a catastrophic breakdown of a critical conveyor belt, causing a complete shutdown and severe production delays. The breakage occurred due to a combination of excessive mechanical stress and material defects.
Impact: The incident resulted in substantial financial losses from lost production and repair costs. Additionally, the plant faced safety concerns for employees working near the damaged belt.
Case Study: Environmental Extremes
Incident: An offshore oil platform endured severe storms, resulting in extensive damage to subsea pipelines. The breakage occurred due to prolonged exposure to high winds and waves, which weakened the pipeline materials.
Impact: The breakage led to operational inefficiencies, high repair costs, and environmental hazards from potential oil spills. The incident highlighted the importance of considering environmental factors in breakage prevention.
Case Study: Human Error
Incident: During a construction project, a crane operator accidentally dropped a heavy beam onto a newly installed glass curtain wall. The breakage resulted from a momentary lapse in attention.
Impact: The incident caused costly repairs to the curtain wall and delayed the completion of the building. It emphasized the crucial role of human factors in breakage prevention and the need for proper training and supervision.
Best Practices for Breakage Management
The aforementioned case studies provide valuable lessons on the consequences of breakage and the importance of implementing effective management strategies. Here are several best practices that organizations can adopt to minimize breakage and its associated risks:
1. Enhanced Design and Engineering:
- Conducting thorough stress analyses and simulations
- Utilizing durable materials and advanced manufacturing techniques
- Ensuring proper maintenance schedules and inspection protocols
2. Quality Materials and Manufacturing:
- Sourcing high-quality materials from reputable suppliers
- Employing stringent quality control measures throughout the manufacturing process
- Implementing robust packaging and storage practices
3. Regular Inspection and Maintenance:
- Establishing comprehensive inspection and maintenance plans
- Utilizing advanced non-destructive testing techniques to detect potential defects early on
- Conducting preventive maintenance to address wear and tear before they escalate into breakage
Related Topics:
- [Seo Optimized Title]: Expressing “Outside” In Spanish: Essential Phrases, Nouns, Verbs, And Adjectives
- Easy Guide To Pronouncing Prairie: Mastering The Correct Syllables
- Discover The Origins And Impact Of The Surname Braden
- How To Pronounce “Posolé”
- Ultimate Guide To Pronouncing Laos: A Step-By-Step Breakdown