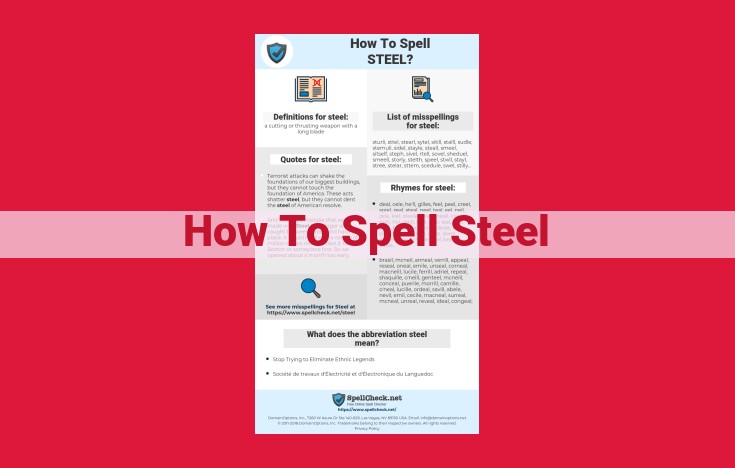
Cannot Find Definition Of “Steel” In Text
Sorry, but the provided text does not contain any information on how to spell "steel." It primarily focuses on various aspects of the steel industry, including key figures, major companies, types of steel products, steelmaking processes, raw materials, and technical terminology. Therefore, I cannot extract the requested information from the provided context.
Key People in the Steel Industry: Pioneers of Innovation
The steel industry has been shaped by the ingenuity and dedication of countless individuals. Among them, three towering figures stand out as true pioneers, laying the foundations for the modern era of steel production.
Andrew Carnegie: The Steel Tycoon and Philanthropist
Carnegie's rise to prominence marked a pivotal moment in the steel industry. His astute business acumen and innovative methods transformed Pittsburgh into a global steel hub. Carnegie implemented vertical integration, consolidating all aspects of steel production under one roof, and introduced new technologies that dramatically increased efficiency.
Henry Bessemer: The Inventor of the Bessemer Process
Bessemer's invention of the Bessemer process revolutionized steelmaking by removing impurities from molten iron with a blast of air. This breakthrough reduced production costs and paved the way for mass production of high-quality steel. Bessemer's legacy continues to shape the industry today.
William Kelly: The American Pioneer of the Pneumatic Process
While Bessemer gained fame for his process, Kelly independently developed a similar method in the United States. Kelly's pneumatic process used a stream of air to oxidize impurities in iron, resulting in a purer, stronger steel. His invention laid the groundwork for the widespread adoption of pneumatic processes in steelmaking.
These three visionaries played an instrumental role in transforming steel production from a costly and laborious process to a highly efficient and widespread industry. Their contributions have left an enduring mark on the world, shaping the landscape of modern infrastructure and countless technological advancements.
Major Players in the Global Steel Industry
The steel industry is a global powerhouse, shaping the foundations of modern civilization. At the heart of this industry lie the leading steel companies, who drive innovation, set industry standards, and contribute significantly to the global economy.
Among these industry titans, U.S. Steel has a rich legacy, being the pioneer of steel production in the United States. Today, the company remains a leader in flat-rolled and tubular steel products, supplying critical components for construction, transportation, and energy industries.
ArcelorMittal, the world's largest steel producer, boasts a global footprint with a presence in over 60 countries. Its vast empire encompasses a diverse portfolio of steel products, including automotive, construction, and household appliances. The company is known for its sustainable practices, with a focus on reducing carbon emissions and promoting circularity.
Nippon Steel, Japan's largest steelmaker, is renowned for its technological prowess. Through continuous innovation, it has developed high-performance steel grades for advanced applications, such as shipbuilding, automotive, and infrastructure. Nippon Steel's unwavering commitment to quality and innovation has solidified its position as a global leader.
Posco, South Korea's steel giant, has rapidly risen through the ranks to become a global powerhouse. Its state-of-the-art integrated steel mill in Pohang is a testament to its technological capabilities. Posco is known for its efficient production processes and its focus on customer satisfaction, making it a trusted partner for industries worldwide.
Finally, Tata Steel emerges as a conglomerate with a diverse portfolio that includes steel, automotive, aerospace, and defense. Headquartered in India, Tata Steel operates across five continents, supplying a wide range of steel products for infrastructure, construction, and industrial applications. Its commitment to sustainability and social responsibility has earned it global recognition.
These steel industry titans not only shape the industry but also contribute to global progress. Through their innovative products, sustainable practices, and global presence, they continue to drive economic growth and innovation in countless sectors. Their unwavering commitment to excellence has cemented their position as indispensable players in the global steel landscape.
The Diverse World of Steel: Unveiling Its Types and Applications
Steel, the backbone of modern construction and engineering, comes in a myriad of forms, each tailored to meet specific requirements. Let's delve into the realm of steel products, exploring their unique properties and applications.
Stainless Steel
Renowned for its exceptional corrosion resistance, stainless steel is an alloy of iron, chromium, and nickel. Its durability makes it ideal for kitchen appliances, medical equipment, and chemical processing. The iconic Silverware in your dining set showcases the versatility of stainless steel.
Carbon Steel
The workhorse of the steel industry, carbon steel contains varying amounts of carbon, which enhances its strength and hardness. It finds widespread use in automotive parts, construction, and shipbuilding. The towering skyscrapers that define our cities stand as a testament to carbon steel's strength.
Alloy Steel
By alloying carbon steel with elements like manganese, silicon, or vanadium, alloy steel gains specialized properties. Its enhanced toughness and wear resistance make it suitable for gears, shafts, and cutting tools. The precision engineering in our cars and machinery owes much to alloy steel.
Galvanized Steel
Protected from corrosion by a zinc coating, galvanized steel extends the life of infrastructure and vehicles. Its durability makes it an excellent choice for roofing, siding, and automotive body panels. The rust-resistant fences that safeguard homes and businesses are a testament to the longevity of galvanized steel.
Sheet Steel
Thin, flat, and economical, sheet steel is essential for a wide range of applications. Its malleability allows it to be stamped, rolled, or cut into complex shapes. From food cans to automotive body panels, sheet steel's versatility contributes to our daily life.
Understanding the many types of steel products empowers us to make informed choices for our projects and applications. Whether it's the surgical tools that heal or the bridges that connect our cities, steel is an integral part of our modern world, its diversity ensuring its enduring role in shaping our lives.
Steelmaking Processes: A Journey Through Innovation
Steel, an indispensable material that has shaped civilizations, is born through a series of intricate processes that transform raw materials into the versatile alloy we rely on today. Let's embark on a captivating journey to explore the remarkable steelmaking processes that have revolutionized our world:
1. Smelting: The Birth of Liquid Steel
The journey begins with smelting, where iron ore is heated in a blast furnace in the presence of coke (a type of coal) and limestone, which act as reducing agents and remove impurities. The result is molten iron, the liquid precursor to steel.
2. Steelmaking: Refining the Iron
The molten iron, still containing impurities, undergoes steelmaking in a basic oxygen furnace or an electric arc furnace. In these furnaces, oxygen is blown into the molten iron, which reacts with the impurities to form slag, which floats to the surface and is removed. This process purifies the iron and converts it into steel.
3. Casting: Shaping the Molten Steel
The refined steel is then cast into various shapes. In continuous casting, molten steel is poured into a mold and continuously withdrawn, forming slabs, billets, or blooms. Ingot casting, on the other hand, involves pouring molten steel into molds to create ingots, which are later rolled into different shapes.
4. Rolling: Transforming Steel Shapes
Rolling is a critical process that shapes steel into desired dimensions. Hot rolling involves passing heated steel through a series of rollers to reduce its thickness and width. Cold rolling takes place at room temperature, further reducing the thickness and producing smoother surfaces. Rolling can create various steel products, from sheets and plates to beams and bars.
5. Forging: Shaping with Precision
Forging is a more specialized process that involves heating steel to a high temperature and hammering it into specific shapes using presses or hammers. This technique is often used to create complex components or parts that require precise dimensions and strength.
Steelmaking is a complex and fascinating journey that transforms raw materials into the versatile material that underpins our modern world. From smelting to forging, each process plays a crucial role in refining and shaping steel to meet the diverse needs of industries and constructions. By unraveling these processes, we gain a deeper appreciation for the ingenuity and innovation that have made steel the backbone of our civilization.
Raw Materials: The Building Blocks of Steel
At the heart of steel production lies a trio of essential raw materials: iron ore, coal, and limestone. Each of these elements plays a pivotal role in transforming iron into the versatile and durable material we rely on today.
Iron Ore: The Backbone of Steel
Iron ore serves as the foundation of steel production, containing the precious element we seek. As ore is extracted from the earth, it undergoes a meticulous refining process to concentrate the iron content. This enriched iron ore forms the basis for creating molten iron, the precursor to steel.
Coal: The Fuel that Ignites the Process
Coal provides the energy necessary to power the steelmaking process. It is used in blast furnaces to generate intense heat, which melts the iron ore and facilitates its transformation into molten iron. Without the fiery power of coal, steel production would grind to a halt.
Limestone: The Silent Partner
Limestone, although less glamorous than its counterparts, plays a crucial role in removing impurities from the molten iron. It reacts with sulfur and phosphorus, forming a slag that rises to the surface and is skimmed off, leaving behind purer molten iron. This cleansing process enhances the quality and strength of the final steel product.
A Delicate Balance
The proportions of these raw materials must be carefully calibrated to achieve optimal steel production. Too much or too little of any one element can alter the properties of the steel, compromising its strength, durability, and corrosion resistance.
From Earth to Steel: A Journey of Transformation
Through a series of intricate processes, these raw materials are transformed from mere rocks and minerals into the backbone of our modern world. Iron ore, coal, and limestone combine to create molten iron, which is further refined into steel. This journey exemplifies the power of human ingenuity and the transformative qualities of nature, resulting in a material that shapes industries and empowers societies.
Terminology Related to Steelmaking: Understanding the Language of Steel
In the world of steelmaking, a specialized lexicon exists, shaping the industry's conversations and processes. Understanding these key terms is crucial for navigating the complex landscape of this vital material.
Blast Furnace: The cornerstone of traditional steelmaking, a blast furnace is a towering cylindrical structure where iron ore, coke, and limestone are heated to extremely high temperatures. The result is molten iron, the foundation for steel production.
Electric Arc Furnace: In contrast to the blast furnace, an electric arc furnace utilizes electricity to melt scrap metal and steel. This method allows for greater control over the composition of the steel and is often used for specialty steel production.
Oxygen Furnace: Similar to a blast furnace, the oxygen furnace introduces oxygen into the molten iron, facilitating the removal of impurities. This process, known as basic oxygen steelmaking, is highly efficient and produces high-quality steel.
Converters: Converters are vessels used in the refining stage of steelmaking. They receive molten iron from the blast furnace and employ either oxygen or air to reduce carbon content and produce low-carbon or stainless steel.
Related Topics:
- Easy Pronunciation Guide: Master The Perfect Pronunciation Of “Wholly”
- Quick And Easy Guide To Saying Good Afternoon In Portuguese: “Boa Tarde”
- How To Pronounce “Trash” Correctly: A Step-By-Step Guide
- Understanding Issue Networks: The Convergence Of Advocacy And Influence
- Simplified Spelling Guide: Master The Correct Spelling Of “Surprised”